The 4-Minute Rule for Alcast Company
The 4-Minute Rule for Alcast Company
Blog Article
Alcast Company Fundamentals Explained
Table of ContentsThe 7-Minute Rule for Alcast CompanyThe smart Trick of Alcast Company That Nobody is Talking AboutAlcast Company Fundamentals Explained7 Easy Facts About Alcast Company DescribedAlcast Company Fundamentals Explained8 Simple Techniques For Alcast Company
The subtle difference lies in the chemical material. Chemical Contrast of Cast Aluminum Alloys Silicon promotes castability by decreasing the alloy's melting temperature level and boosting fluidness throughout casting. It plays a critical duty in permitting intricate mold and mildews to be filled accurately. Additionally, silicon contributes to the alloy's strength and wear resistance, making it important in applications where toughness is essential, such as automobile components and engine elements.It likewise enhances the machinability of the alloy, making it easier to process right into completed items. In this means, iron contributes to the total workability of aluminum alloys.
Manganese adds to the toughness of light weight aluminum alloys and improves workability. Magnesium is a light-weight component that gives stamina and influence resistance to aluminum alloys.
How Alcast Company can Save You Time, Stress, and Money.
Zinc improves the castability of aluminum alloys and helps control the solidification procedure during spreading. It boosts the alloy's toughness and solidity.
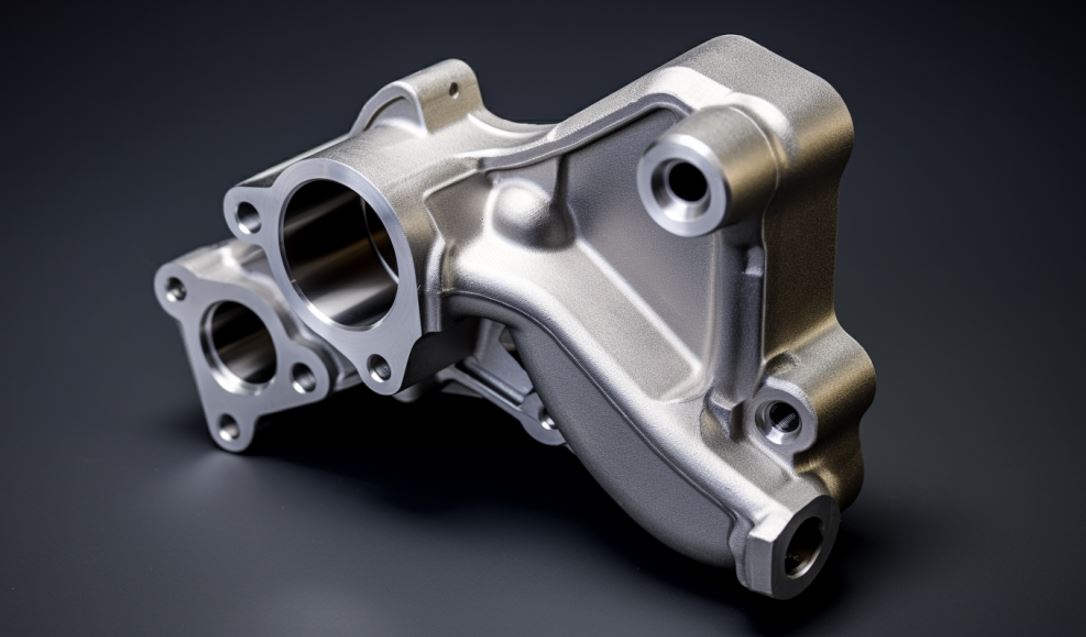
The main thermal conductivity, tensile toughness, return toughness, and elongation differ. Among the above alloys, A356 has the highest thermal conductivity, and A380 and ADC12 have the least expensive.
Alcast Company - Truths
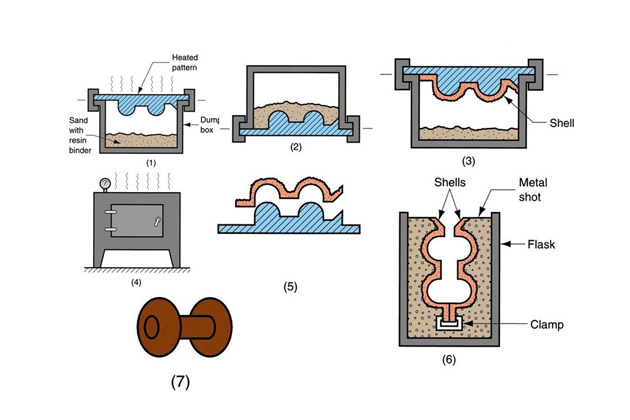
In accuracy casting, 6063 is fit for applications where intricate geometries and high-quality surface area finishes are vital. Examples include telecommunication enclosures, where the alloy's exceptional formability enables smooth and visually pleasing styles while maintaining architectural honesty. Likewise, in the Illumination Solutions industry, precision-cast 6063 components produce stylish and reliable lights fixtures that need detailed shapes and excellent thermal performance.
The A360 shows remarkable elongation, making it excellent for facility and thin-walled parts. In accuracy casting applications, A360 is well-suited for sectors such as Consumer Electronics, Telecommunication, and Power Tools.
Fascination About Alcast Company
Its unique properties make A360 a valuable choice for accuracy casting in these markets, improving item resilience and quality. Aluminum alloy 380, or A380, is a widely used spreading alloy with several distinctive characteristics. read what he said It offers excellent castability, making it an optimal selection for accuracy casting. A380 shows excellent fluidity when molten, guaranteeing complex and thorough mold and mildews are accurately reproduced.
In accuracy spreading, aluminum 413 radiates in the Consumer Electronics and Power Equipment sectors. This alloy's premium corrosion resistance makes it an exceptional selection for outdoor applications, guaranteeing long-lasting, resilient products in the pointed out industries.
Alcast Company Fundamentals Explained
Once you have determined that the light weight aluminum die casting process appropriates for your task, an essential next step is determining on the most appropriate alloy. The light weight aluminum alloy you pick will considerably influence both the spreading procedure and the homes of the end product. Due to this, you have to make your choice meticulously and take an informed approach.
Establishing the most ideal light weight aluminum alloy for your application will imply weighing a vast array of qualities. The first classification addresses alloy features that affect the production process.
6 Easy Facts About Alcast Company Explained
The alloy you pick for die casting directly affects several aspects of the casting process, like exactly how simple the alloy is to collaborate with and if it is vulnerable to casting issues. Warm cracking, also referred to as solidification breaking, is a typical die spreading issue for aluminum alloys that can cause inner or surface-level tears or cracks.
Particular aluminum alloys are more vulnerable to warm fracturing than others, and your option ought to consider this. It can harm both the cast and the die, so you should look for alloys with high anti-soldering homes.
Deterioration resistance, which is currently a noteworthy characteristic of light weight aluminum, can differ significantly from alloy to alloy and is a necessary characteristic to think about depending on the ecological conditions your item will be exposed to (Casting Foundry). Wear resistance is an additional residential property frequently sought in light weight aluminum items and can distinguish some alloys
Report this page